Building Orion
By Tom Jones|November 2016
NASA prepares its deep-space module to fly past the moon
At Kennedy Space Center in Florida, Lockheed Martin has begun assembling an Orion crew vehicle for an ambitious but unmanned flight beyond the moon in late 2018. The NASA team faces challenging development and test milestones to execute Exploration Mission-1, which will be a far more difficult test flight than 2014’s five-hour-long Exploration Flight Test-1.
EM-1 will last up to three weeks to check out Orion’s most critical systems in a deep-space environment. This will be the first human-capable spacecraft to reach lunar orbit since 1972, and will journey farther from Earth than any Apollo crew. A successful EM-1 will be a giant step toward launching astronauts on their own lunar orbit journey in 2021.
Orion explained
Orion will be NASA’s deep-space workhorse for the next three decades. In independent flight, it carries enough propellant, oxygen and water to reach lunar orbit with a crew of four, on missions lasting about three weeks. For journeys to near-Earth asteroids or the Mars system, Orion would dock with a larger spacecraft incorporating a habitat, propulsion and power modules.
Each Orion spacecraft will consist of three major components from top to bottom: a launch abort system, the crew module and the service module, all launching atop a Space Launch System booster. The launch abort system, or LAS, can respond within milliseconds to a launch emergency and rocket the crew module free of its failing booster and onto a proper splashdown trajectory. After the 400,000-pound thrust abort motor burns out, a jettison motor then pulls clear the spent rocket and protective shroud, positioning the crew module for parachute deployment.
The LAS shroud shelters the crew module, which provides living space for up to four astronauts and protects them from the deep-space environment during missions lasting as long as three weeks. Recovery parachutes surround the nose docking hatch, while at the base is a titanium-and-composite heat shield, covered with ablative Avcoat resin to protect the module from peak re-entry temperatures of 5,000 degrees Fahrenheit (2,760 Celsius).
The crew module contains four seats that the astronauts will fold and stow after launch. “Orion won’t be a roomy ship, but it does have 150 percent more elbow room than Apollo,” says Rick Mastracchio, the astronaut office’s representative to the Orion program. The galley is spartan, with just a water dispenser and food warming case. Nearby is a small, resistive exercise machine. Tucked into the lower deck will be a very compact toilet compartment, rigged with pop-up curtains to preserve a modicum of privacy.
Another astronaut working on Orion, Lee Morin, leads the Rapid Prototyping Lab at Johnson Space Center, which is tasked with producing the crew displays. Orion will have three computer monitors, whose screens can be divided into two displays. The space shuttle’s more than a thousand switches and gauges have been reduced in Orion to just 60 or so for controlling emergency and lighting systems; the only gauge will be a combination voltmeter-altimeter. To control the spacecraft, the crew can bring up any of the 70 to 90 interactive displays being planned by using some of the 30 keys around each monitor’s bezel. When the g-forces of launch and re-entry make it difficult or impossible to reach the bezel keys, the crew can command the ship through a seat-mounted cursor device, using only the forefinger on the left glove. Morin’s team knows these displays and software are in the spotlight: They must be delivered to Lockheed Martin by March 2019 to support the first crew launch — EM-2 — in 2021.
Service module in critical path
Beneath the crew module heat shield is the 13,500 kilogram service module, which houses propulsion, attitude control, thermal control and electrical power systems, and also carries oxygen, nitrogen and water tanks to sustain the crew. This module is being built by the European Space Agency based on the design of its Automated Transfer Vehicle, which made five supply runs to the International Space Station. Europe is contributing the module under a barter arrangement with NASA to fulfill its share of ISS operating costs through 2020. NASA has consciously placed the service module in the critical path for Orion, hoping to cement a NASA-European relationship for exploring deep space. “We will need partners to get to Mars. It’s our intent to keep ESA involved for the duration of the Orion program,” says Mark Kirasich, NASA’s Orion program manager.
Because fuel cell-generated electricity (using tanks of oxygen and hydrogen reactants, as on Apollo and the shuttle) is impractical for Orion’s long missions, the service module gets its power from the Sun. Four arrays spanning 19 meters gather solar energy and store enough of it in lithium ion batteries to power Orion through 90 minutes of eclipse (in the moon’s shadow, for instance).
The module’s single main engine will be a repurposed shuttle Orbital Maneuvering System engine, producing 26,690 newtons of thrust for deep space maneuvers or entering and leaving orbit. This pressure-fed Aerojet Rocketdyne design flew 30 years of shuttle missions without a failure. For Orion, each engine will fly with new propellant lines and tanks. Kirasich says NASA will fly out the existing inventory of shuttle OMS engines, then build new ones starting in the 2020s.
Assembling Orion
Exploration Flight Test-1 in 2014 proved that Orion’s crew module could withstand launch, the space environment and re-entry from a high Earth orbit.
Its heat shield protected the crew module as it re-
entered at a near-lunar return speed of 32,187 kilometers per hour. After recovery from the ocean off southern California, Orion’s performance, structure and systems were assessed in preparation for building the EM-1 crew module. By analyzing flight loads and improving manufacturing efficiency, engineers reduced the mass of the crew and service modules by 1,590 kilograms, including 365 kilograms of structural weight, says Jules Schneider, senior Orion operations manager for Lockheed Martin’s assembly team at Kennedy Space Center. The number of welds needed to build the crew module’s pressure vessel, for example, was reduced from 33 to seven.
“We’ve completed the build of the pressure shell and secondary structure; now we’re inside the clean room to install the propulsion system, thruster valves, helium lines, and the fluid lines for the propylene glycol and ammonia cooling systems,” Schneider says. He and his team must deliver the EM-1 spacecraft to Kennedy’s ground operations group in the first quarter of 2018, so they can integrate the spacecraft onto the SLS booster.
Manufacturing and EFT-1 flight experience has helped improve and streamline the building of the heat shield. Instead of curing the ablative Avcoat resin in a monolithic honeycomb layer covering the composite heat shield structure, Lockheed Martin for EM-1 will bond 180 separate blocks of Avcoat-filled honeycomb to the back shell. The new heat shield build-up, to be completed at Kennedy, will allow more precise control of the curing process, meet all structural strength requirements for future Orion missions, shorten manufacturing time by two months and save money.
Schneider says that after the clean room work, the crew module will receive its wiring, electronics and batteries in preparation for power-up of the crew module in February or March 2017. Meanwhile, the front and back sections of the service module will come together at Kennedy by March or April 2017, followed by separate testing of crew and service modules before umbilical connections tie them together.
The entire EM-1 Orion will then be flown to Glenn Research Center’s Plum Brook Station for a crucial two months of environmental tests. In Plum Brook’s mammoth thermal-vacuum chamber, the ship will be cooled to minus 20 degrees Fahrenheit and baked at 150 degrees to verify the function of its pressurization, insulation and thermal control systems. After acceptance tests back in Florida, Orion will then go through hypergolic propellant loading, installation of the launch abort system atop the crew module, and stacking atop the SLS booster in the Vehicle Assemble Building. The EM-1 launch is planned for sometime during the last three months of 2018.
The tempo at the Orion assembly line in Kennedy’s Armstrong Operations and Checkout Building is quickening. Assembly of the crew module structural test article, intended for intensive loads testing at Lockheed Martin in Denver, starts in November. In March, Lockheed Martin will begin construction at Kennedy of the EM-2 crew module, which will carry the first Orion crew in 2021.
Exploration Mission One
EM-1 in 2018 will be the first flight of the heavy-lift Space Launch System booster. Its upper, Interim Cryogenic Stage will propel Orion out of low Earth orbit on a 21-day flight designed to prove the spacecraft can safely support a crew in deep space. After a weeklong outbound transit, Orion will skim within 100 kilometers of the moon and, firing its main engine, enter a distant retrograde orbit some 70,000 kilometers beyond the lunar far side. After a week of systems tests, another engine firing will drop Orion through a lunar swingby that will steer it toward Earth for re-entry and splashdown. The crew module will enter the atmosphere at 40,500 kph and deploy three main parachutes for a West Coast splashdown and recovery.
“EM-1 was intended to be a dress rehearsal for the EM-2 crewed mission in 2021, but it will be missing some key elements,” says the astronaut office’s Mastracchio. “It won’t have a life support system or crew displays, for example.” The astronauts will be watching EM-1’s results closely. “Where do you draw that line—where you understand the vehicle’s performance well enough to put people aboard on the next flight?”
Orion’s future
Kirasich, the Orion program manager, notes that “on EM-1, Orion will fly farther and longer than Apollo. We want it to be a capable, flexible spacecraft that can take on many classes of exploration missions.” After the first crewed flight, he would like to see NASA fly an Orion mission at least annually, maybe twice a year, but for that “we need more budget.” Orion is funded this fiscal year at $1.27 billion. Through partial reuse and manufacturing efficiencies, Kirasich hopes to drive down production and operations costs to create a funding wedge for more frequent flights. In the mid-2020s, after several piloted test flights, NASA hopes to fly Orion astronauts to lunar orbit to sample a captured asteroid boulder in the piloted portion of the Asteroid Redirect Mission.
What are the program’s big challenges? “Spacecraft mass,” says Kirasich. “EM-1 will not have all of the crew systems, like life support and crew displays, due to both weight and budget.” Lockheed Martin’s Schneider says “the biggest variables for EM-1 will be getting the European service module here on time, and the two months of environmental testing at Plum Brook. That’s making some of us nervous,” he admits, “but we’re going to be ready to go.”
What gets Schneider past the daily frustrations of running an assembly line for NASA’s new spaceship? “I enjoy showing kids a spacecraft that’s going to go around the Moon. Their eyes light right up. It’s good to keep that perspective on things.” ★
Related Topics
Human Spaceflight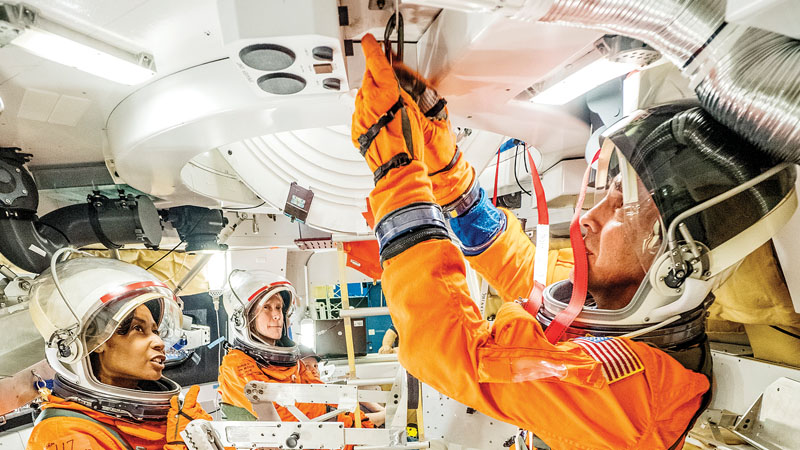
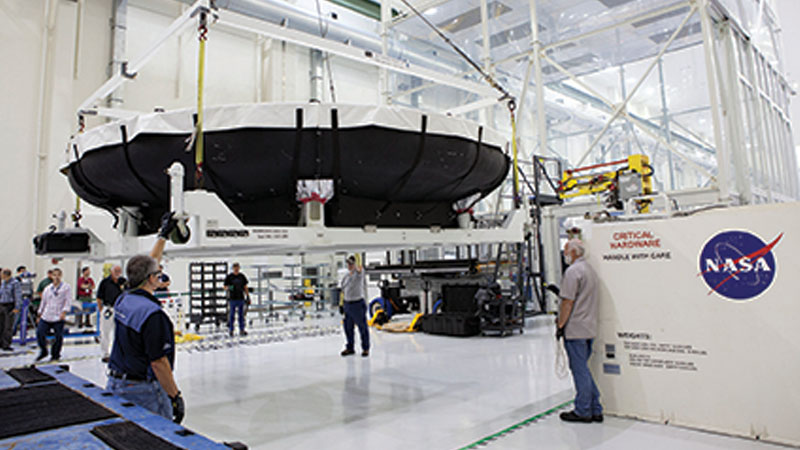
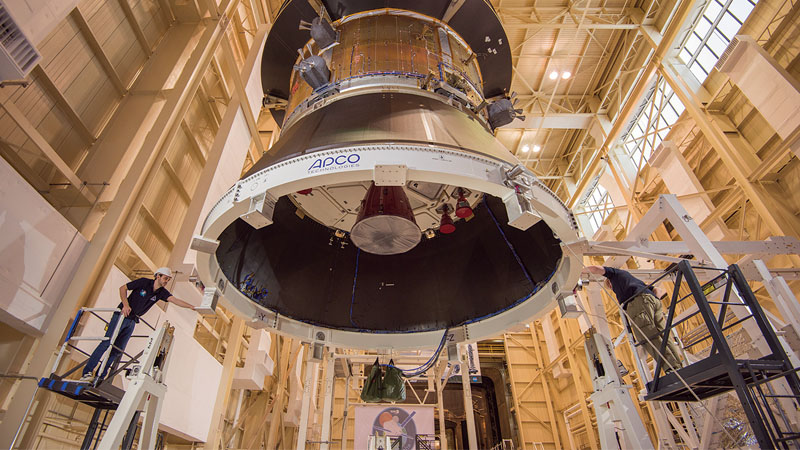
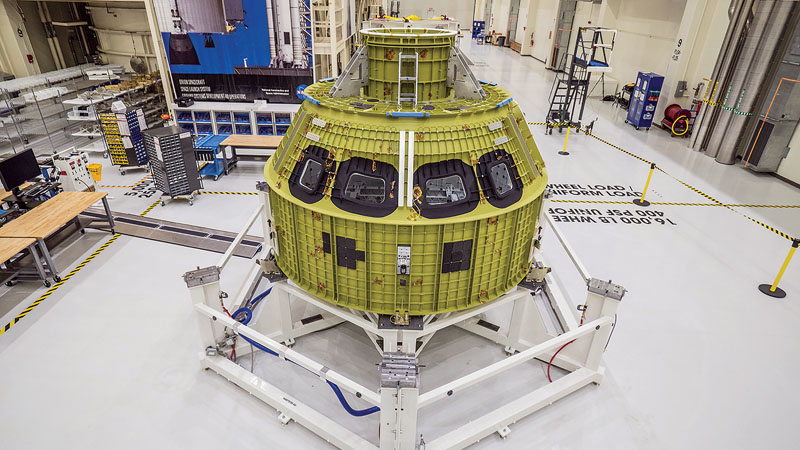